Hinckley is Nigeria’s leading repair and remarketing of used technology products repairing over 1000 items per month. The objective of our remarketing service is to optimise the residual returned to our Clients by operating on a profit share or fixed purchase price mechanism. This is achieved through our dedicated remarketing team located across Nigeria.
Hinckley remarkets equipments nationwide which ensures we are able to optimise the revenue return to our Clients. Hinckley operates an open market in the goods it manages through the use of internet sales channels and dedicated regional sales teams.
– Remarketing Profit Share
The profit share service starts with the receipt of an asset list or inventory from a client with details of the equipment specification, quantities and location. A forecast of resale values is provided in advance. On arrival at Hinckley, equipment is subject to core technical processing tasks to determine the resale value of equipment.
These core tasks include electrical safety (PAT) testing, testing the functionality of the equipment, data wiping using approved software and cosmetic grading and assessment. Successfully processed equipment is then sold through Hinckley’s established remarketing channels. Hinckley reports monthly values achieved from the resale of
equipment.
– Buyback
The buyback solution is focused on generating best in market values from used equipment whilst delivering clients data protection and environmental regulatory compliance and demonstrating sustainability & corporate social responsibility.
Equipment which meets the functional and cosmetic requirements will be purchased
based on an agreed value in advance inclusive of all costs subject to functionality and
condition at time of processing.
Starting with receipt of an asset list or inventory from a client with details of the specification and quantities, a buyback quotation will be issued detailing the purchase price of each item in advance. On arrival at Hinckley, equipment is subject to core technical processing tasks to determine the final purchase price of equipment. These core tasks include electrical safety (PAT) testing, testing the functionality of the equipment, data wiping using approved software and cosmetic grading and assessment. Successfully processed equipment is then sold through Hinckley’s established remarketing channels. Hinckley reports the condition of each item and final purchase price.
The buyback service allows organisations to identify the budget across a range of equipments and over a given time scale.
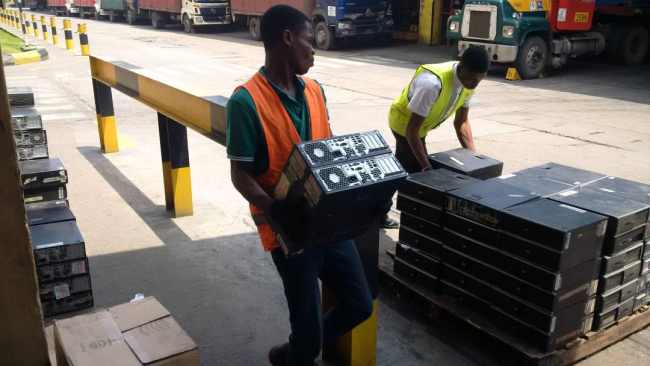
Certification
As part of Hinckley’s core processing tasks, all data bearing items are data wiped using approved software. Subject to safety testing and functionality checks this key task allows successfully data wiped equipment to be sold for reuse generating residual value.
Degaussing
Where hard disk drives and other magnetic media will not be reused, these are passed through approved degaussing tools which destroy all data and makes reuse impossible.
Disintegration
Often referred to as shredding, this process is employed where hard disk drives and other data bearing devices cannot be successfully wiped or where it has been decided that equipment cannot be reused.
- Data bearing devices including hard drives are shredded down to 25mm strips
- These strips are sent for smelting where precious metals are extracted
- 0% of these strips end up in landfill, all metals are recycled.